No sooner do I lean my bike against the fence than Matt Larsen glances down and says, “Your tires are on backwards.” Sure enough, when I mounted my tires, I overlooked the arrow pointing out the intended rotational direction. Leave it to a wheel builder to spot that right away. We joked about how all my Strava miles are actually in the negative now and he offered to remount the tires for me. After all, he had the tools right there in his shop. I thanked him but declined. I will ride home in shame and put them on correctly, as I should have done in the first place.
A row of rims stretches across the ceiling of the garage Larsen converted into a shop. He is patiently yet quickly assembling a bicycle wheel. He inserts one spoke after another through the spoke flange on the hub and into the rim. He attaches a nipple to each and tightens them just enough to keep the parts together. Once all the spokes are in, he puts the wheel in the truing stand and tightens each nipple until all the threads on each spoke have disappeared. As the slack from the loose spokes is removed, the wheel tightens up and he must use a spoke wrench on the last few nipples to get them as flush as the others.
Larsen explains the four factors that concern him. He needs to maintain the round of the rim. That means the rim’s shape is that of a circle with the hub in the center. Next, there must be no movement to either side as the wheel spins. Third is the dish. The rim must be centered on the hub, which is not necessarily the same as centered on the spoke flanges. This ensures the cassette and disc brakes, which also occupy space on the hub, are taken into account. Last of all, the tension on the spokes must be balanced. All these pulling and pushing forces are adjusted until the wheel is rigid and remains so.
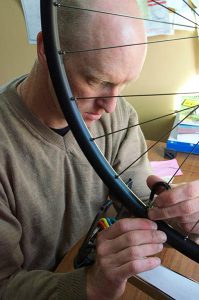
After working as a mechanic at several bike shops, Larsen wound up at a bike parts wholesaler. Along with shipping bike parts, the company also sold hand-built wheels, which interested Larsen. He learned how to build wheels and gained a lot of experience. The company laid him off when the economy went south in 2007, so Larsen decided to put his experience to use for himself. He opened his own accounts with suppliers, established a website, and jumped into the wheel-building business with both feet.
In 2012, Larsen moved to Spokane where he was pleasantly surprised by its large and active cycling community. As a result, Spokane has been a good fit for him. Larsen has established business relationships with local bike shops and local bike builder Glen Copus of Elephant Bikes. Through his website, Larsen’s customers are located across the United States and into Canada and Europe. But local customers get a bonus through their personal relationship with the guy who built their wheels. And they can bring their wheels in for free truing.
Why invest in hand-built wheels? If your rims are worn out or damaged, you can save money by using the hubs from those wheels as the foundation for new ones. The hub is the most expensive part and can last for many years. Or you may want something lighter because you race. Perhaps you need a beefier configuration because you go on punishing rides. Or maybe you want your hubs or rims to have a specific color that matches your frame. Overall, the main benefit of hand-built wheels is that you get exactly what you want.
The bicycle industry has a small profit margin and Larsen jokes that he chose the wrong business model because he builds a product that will last 10 years. His customers return because he provides quality service and quality products. Meeting his customers’ needs is his primary goal. His local customers can interact with him personally at a race, a bike exposition, or at his shop. Even if he just needs to point out that your tires are on backwards. For more information, visit www.mlwheels.com. //